Simulatori di processo
Con origine negli anni sessanta (creati all'interno di societa' quali MW-Kellog, Union Carbide etc.) , inizialmente per lo studio dei processi di separazione (colonne di distillazione) , i sistemi di simulazione hanno visto le loro capacita' crescere parallelamente alla potenza dei calcolatori e dei sistemi operativi disponibili.
Ai nostri giorni l'affermazione dei personal computers consente ad ogni progettista di disporre di un sofisticato centro di calcolo sul proprio tavolo di lavoro.
Principali caratteristiche
I sistemi di simulazione consentono di modellare il comportamento di interi impianti calcolando le condizioni raggiunte in una serie di punti (ad esempio all'ingresso ed uscita di apparecchiature) in una determinata condizione operativa.
Generalmente l'intero sistema viene risolto per una predefinita condizione di marcia (espressa in termini di portate, temperature, pressioni, composizioni delle correnti) quindi a regime continuo, i sistemi di simulazione che consentono di identificare questa condizione vengono definiti (per analogia) "steady-state" e risultano essere i piu' diffusi.
Invece i sistemi in grado di calcolare in successione una serie di condizioni di marcia vengono generalmente definiti simulatori dinamici, questi consentono di studiare le problematiche legate a variazioni delle condizioni nel tempo (avviamenti, fermate, cambiamenti di marcia, sistemi ciclici, emergenze etc.).
E' opportuno notare come, in pratica, molte simulazioni di condizioni transitorie possono essere risolte anche con i sistemi steady-state ad esempio operando per successivi punti operativi (integrazione diretta). Vi sono tuttavia delle aree, ad esempio una colonna od un reattore operati in modo discontinuo, dove la disponibilita' di appositi algoritmi risolutivi offre indubbi vantaggi nel calcolo. Altre procedure spesso fatte rientrare nel campo dell'analisi dinamica, ad esempio la depressurizzazione di un recipiente, vengono frequentemente risolte con metodi di integrazione diretta.
In ogni caso, in entrambi i sistemi (steady state o dinamici) la simulazione consiste in una serie di calcoli per risolvere l'insieme di equazioni rappresentanti le caratteristiche delle varie componenti dell'impianto, nei simulatori sono comunemente inclusi tre tipi di strutture di calcolo:
- Package per la stima delle proprieta' dei fluidi
- Moduli di calcolo
- Sistema risolvitore
Package per la stima delle proprita' dei fluidi
Ha il compito di eseguire i calcoli per la stima delle proprieta' termofisiche (trasporto, equilibrio etc.) deicomposti presenti nell'impianto. Il package include normalmente una banca dati con le proprieta' dei componenti puri, di esteso impiego sono le correlazioni sviluppate da DIPPR (vedi sezione banche dati). Per il calcolo dei valori di equilibrio (e la correzione dei valori di entalpia , entropia etc.) nel package sono generalmente inclusi modelli termodinamici basati su equazioni di stato e derivazioni dell'equazione Gibbs-Duhem (Wilson, NRTL, Uniquac etc.) questi generalmente consentono di affrontare la maggior parte dei casi operativi.
Moduli di calcolo
Si tratta di procedure che includono algoritmi in grado di caratterizzare il funzionamento di differenti componenti quali colonne, scambiatori, pompe etc. Il modulo piu' importante (ed utilizzato) e' il modulo flash che costituisce la base di tutti i calcoli termodinamici. Altri importanti moduli sono la colonna (in grado di simulare una intera colonna di separazione) , il reattore, le linee etc.
Modulo Flash
Il modulo Flash simula uno stadio di separazione dove una corrente viene portata dalle condizioni iniziali (pressione, temperatura, composizione) alle condizioni finali specificate in termini di temperatura, pressione, composizione (vapore, liquido), entalpia, entropia. La procedura identifica le condizioni di equilibrio (vapore, liquido) per la corrente in uscita. Le equazioni applicate nel modulo Flash sono:
- V + L - F = 0 (bilancio materia totale)
- V*yi + L*xi - F*zi = 0 (bilancio materia per componente)
- K*xi - yi = 0 (relazione equilibrio)
- SUM(yi - xi) = 0 (somma componenti)
- V*Hv + L*Hl - F*Hf + Q = 0 (bilancio energia, in termini di entalpia o entropia)
Il sistema viene generalmente risolto applicando il metodo Newton dopo aver provveduto ad inizializzare opportunamente le differenti variabili. In funzione delle condizioni specificate per la corrente in uscita si possono identificare una serie di comuni operazioni Flash:
- P,T (pressione, temperatura, isotermo)
- P,V (pressione, percentuale vapore)
- P,H (pressione, entalpia, adiabatico)
- P,S (pressione, entropia)
- T,V (temperatura, percentuale vapore)
Altri tipi di Flash sono disponibili nei sistemi di simulazione piu' sofisticati. Applicando una opportuna operazione Flash e' possibile simulare la maggior parte delle componenti di un impianto, ad esempio una valvola di regolazione o sicurezza attraverso un Flash P,H (specificando la pressione in uscita e lo scambio termico, usualmente pari a 0) , uno scambiatore di calore sempre attraverso un Flash P, H (in questo caso, in generale, lo scambio termico sara' diverso da 0) , un compressore attraverso un Flash P, H o P, S etc.
Modulo colonna separazione
I processi di separazione su correnti multicomponente (estrazione, distillazione, assorbimento) vengono storicamente simulati (1893, Sorel) come una serie di stadi di equilibrio con parametri opportunamente definiti, all'inizio impiegando essenzialmente metodi grafici o semplificati (Ponchon 1921, Savarit 1922, McCabe and Thiele 1925, Lewis and Matheson 1932, Thiele and Geddes 1933) e dalla meta' del secolo scorso impiegando i calcolatori elettronici. Attraverso l'impiego dei calcolatori si puo' risolvere in modo rigoroso l'insieme delle equazioni che definiscono le caratteristiche di ciascun stadio della colonna, i vari stadi vengono simulati attraverso una operazione Flash applicando essenzialmente lo stesso insieme di equazioni:
- Bilancio globale materia
- Bilancio materia per componente
- Relazione equilibrio
- Somma componenti
- Bilancio energia
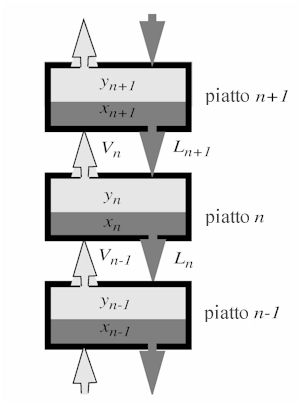
Al momento (anno 2001) i simulatori possono implementare per la modalita' steady-state uno (o entrambi) dei due piu' diffusi algoritmi per simulare colonne di separazione, i due algoritmi si differenziano essenzialmente per il modo con cui vengono stimate le proprieta' dei fluidi:
- Metodo Inside-Out la procedura impiega due sottoprogrammi, nella sezione interna le proprieta' dei fluidi vengono stimate attraverso modelli semplificati e l'intero sistema risolto, la sezione esterna applica i modelli rigorosi e verifica che la soluzione raggiunta sia congruente, nel caso provvede a correggere i modelli semplificati ed attivare per un nuovo ciclo la sezione interna.
- Metodo Simultaneous-Corrections l'intero sistema viene risolto impiegando i modelli rigorosi ed utilizzando il metodo Newton.
Sistema risolvitore
il sistema risolvitore ha il compito identificare lo stato (se esiste) in cui sono raggiunte le condizioni imposte dall'utilizzatore, il comune modo di dire "non converge" significa che il programma non identifica una soluzione ritenuta valida.
Avendo a che fare con un insieme di equazioni non-lineari l'algoritmo risolutivo e' necessariamente di tipo iterativo, calcolando (in sequenza) i dati sui vari moduli sino a convergere ai valori prescritti, i metodi comunemente impiegati sono:
- Metodi quasi-Newton l'intero sistema viene risolto contemporaneamente approssimando le equazioni non-lineari con un sistema di equazioni lineari (Newton), le derivate delle variabili principali (che costituiscono la base dell'insieme di equazioni lineari che definiscono il sistema semplificato) vengono approssimate attraverso il metodo Broyden o equivalenti.
- Metodo sostituzioni successive in questo metodo i risultati precedentemente calcolati vengono reintrodotti come valori di partenza nei successivi cicli di calcolo.
Guida ai prodotti disponibili
Prode distribuisce alcuni dei piu' competitivi prodotti dedicati alla simulazione di processo. I prodotti trattati si caratterizzano per le elevate prestazioni in unione ad un prezzo particolarmente contenuto. Grazie all'esperienza acquisita creando nuovi prodotti software Prode puo' realizzare prodotti su specifiche del cliente.